Understanding Different Types of Benchtop Blast Cabinets
What Are Benchtop Blast Cabinets
A benchtop blast cabinet, also known as a benchtop blasting cabinet, is a smaller and more compact version of a blast room. It is a specialized piece of equipment used for abrasive blasting processes on smaller workpieces or components. As the name suggests, this type of blast cabinet is designed to sit on top of a workbench or table, making it a convenient and space-saving option for various workshops and laboratories. There are several types of benchtop blast cabinets that serve different purposes based on your needs. In this blog post we will cover the four main types and discuss their applications:
- Dry blast cabinets
- Wet blast cabinets
- Lightweight media cabinets
- Tumble cabinets
Dry Blast Cabinets
Traditional dry blast cabinets are a mainstay of production facilities and workshops across the country. Using dry media, these cabinets allow you to focus on smaller parts by manually handling the part and applying the media. Excellent for general cleaning and preparation of components, these cabinets come in varying sizes to accommodate many different sizes of parts that require blasting. Intended to be used all day, every day, dry blast cabinets are ergonomically designed for user comfort, which helps maintain high productivity.
Rapid and Efficient Cleaning: Dry blasting is highly effective in quickly removing various contaminants, such as rust, scale, old paint, and stubborn coatings, from surfaces. It can significantly reduce preparation time before painting or coating applications.
Strong Surface Profiling: Dry blasting generates a more aggressive and deeper surface profile compared to wet blasting. This is particularly beneficial for applications that require strong mechanical adhesion, such as coatings and adhesives.
Wide Range of Abrasive Media: Dry blasting can use a wide variety of abrasive media. The ability to choose different media types and sizes allows for versatility in surface preparation and finishing.
Portability and Flexibility: Dry blasting equipment is generally more portable and easier to set up compared to wet blasting systems. This makes it a suitable choice for various on-site applications, including industrial maintenance, construction, and surface restoration.
Removal of Tough Contaminants: Dry blasting is often the preferred method for removing heavy corrosion, thick paint layers, and coatings from sturdy surfaces.
Enhanced Visibility: Unlike wet blasting, which creates a slurry, dry blasting generates less debris and does not involve water. This provides better visibility during the blasting process, allowing operators to monitor and control the cleaning more effectively.
Minimal Cleanup: Since dry blasting generates less waste in the form of a slurry, cleanup and disposal of spent abrasive materials can be more straightforward compared to wet blasting.
No Drying Time Required: After dry blasting, surfaces are immediately ready for further processing, such as coating or painting, as there is no residual water that needs to dry.
Greater Profile Control: Dry blasting offers more precise control over the surface profile achieved, as the air pressure and media selection can be adjusted to achieve the desired outcome.
Cost-Effective: Dry blasting is generally more cost-effective than wet blasting due to the lower equipment and operating costs. It also requires less abrasive media, which can lead to further savings.
Wet Blast Cabinets
When you’re working with particularly greasy parts, or you need a fine finish on your part that is contaminant free, opt for a wet blast cabinet. For use with a water and media slurry, these cabinets enable you to achieve a superb finish because the water acts as a lubricant, avoiding media impregnation. Wet blasting is less aggressive than dry blasting, making it ideal for cleaning delicate or sensitive surfaces. The addition of water in the process helps cushion the impact of abrasive particles, reducing the risk of damage to the substrate.
Eliminates Dust and Contamination: The water in the wet blasting process suppresses dust and airborne particles, making it a cleaner and safer method for both the operators and the surrounding environment. This is particularly important when working with hazardous materials or in enclosed spaces.
Improved Surface Finish: Wet blasting can provide a smoother and more uniform surface finish compared to dry blasting. The water helps to wash away debris and leaves a cleaner surface, which is particularly beneficial for applications like automotive parts or aerospace components where a pristine finish is required.
Reduced Heat Generation: The presence of water in wet blasting reduces heat buildup during the process. This helps prevent thermal distortion or damage to heat-sensitive materials.
Less Abrasive Consumption: Wet blasting typically uses less abrasive media compared to dry blasting. The abrasive is more efficiently used as the water helps keep the media from fragmenting, resulting in less waste and cost savings.
Versatility in Abrasive Media: Wet blasting can accommodate a wide range of abrasive media, including glass beads, aluminum oxide, plastic, or even organic materials. This versatility allows for tailored applications and surface finishes.
No Static Buildup: Wet blasting does not generate static electricity, which is a common issue in dry blasting. This characteristic is particularly beneficial when working with materials susceptible to static charge-related problems.
Versatility in Applications: Wet blasting is suitable for various applications, including cleaning, surface preparation, paint removal, and even deburring or peening. It can be used on a wide range of materials, such as metals, composites, and plastics.
Less Environmental Impact: The use of water in wet blasting reduces airborne dust and makes it easier to contain and collect the spent abrasive and removed coatings. This can lead to reduced environmental impact compared to traditional dry blasting methods.
Less Noise: Wet blasting tends to produce less noise compared to dry blasting, making it a more operator-friendly process.
Lightweight Media Blast Cabinets
Lightweight media blasting is a specific type of abrasive blasting that uses lighter, softer blasting media. It offers several unique benefits compared to traditional abrasive blasting methods that use heavier media like grit. Here are some of the advantages of lightweight media blasting:
Non-Damaging to Surfaces: Lightweight media blasting is much gentler on surfaces compared to traditional abrasive blasting methods. Soft media effectively removes coatings, contaminants, and oxidation without causing damage to the substrate. It is particularly suitable for delicate or sensitive surfaces, including wood, fiberglass, plastics, and thin metal sheets.
Eco-Friendly and Non-Toxic: Lightweight media does not produce harmful dust or release hazardous materials, making it safer for both operators and the environment.
Less Aggressive on Coatings: Lightweight media blasting is effective at removing various coatings, including paint, rust, grease, and graffiti, without damaging the underlying substrate. This makes it suitable for applications where preserving the original surface is essential.
Multi-Purpose Cleaning: Lightweight media blasting can be used for a wide range of cleaning applications, including automotive restoration, graffiti removal, fire and smoke damage restoration, mold remediation, and more. Its versatility makes it a popular choice in various industries.
Minimal Heat Generation: Lightweight media blasting generates very little heat during the process. This characteristic is beneficial for applications involving heat-sensitive materials, preventing distortion or warping of the substrate.
No Abrasive Embedding: Unlike some other abrasive media, lightweight media is less likely to embed itself into the surface being cleaned. This reduces the need for additional cleaning steps after blasting.
Reduces Surface Preparation Time: Lightweight media blasting can significantly reduce surface preparation time before painting, coating, or refinishing tasks. Its ability to remove coatings and contaminants effectively means less manual effort is required.
Operator-Friendly: Lightweight media blasting generates minimal dust and is less abrasive, leading to reduced operator fatigue and a more comfortable working environment.
Tumble Cabinets
Tumble cabinets, also known as tumble blast cabinets or barrel blast cabinets, are specialized blasting machines used for batch processing of small to medium-sized parts. These cabinets have a rotating drum or barrel that tumbles the parts, exposing them to the blast media from all angles. Tumble cabinets offer several benefits for blasting applications:
Consistent Blasting: Tumble cabinets ensure consistent and uniform blasting of all parts within the batch. The tumbling action of the rotating drum ensures that each part is exposed to the blast media, resulting in even surface preparation and cleaning.
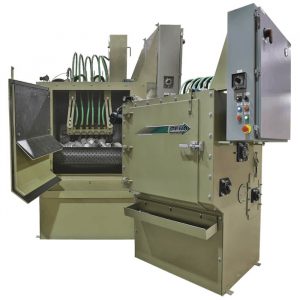
High Efficiency: Tumble cabinets are highly efficient for batch processing. They allow for a large number of parts to be blasted simultaneously, saving time and labor compared to manual blasting methods.
Reduced Labor Costs: With tumble cabinets, operators do not need to individually handle each part during the blasting process. This reduces the need for manual labor and allows operators to focus on other tasks while the parts are being tumbled.
Versatility in Part Size and Shape: Tumble cabinets can accommodate a wide range of part sizes and shapes, as the rotating drum can hold various components within a batch. This versatility makes them suitable for processing small, intricate parts as well as larger, more complex components.
Conserved Blasting Media: The tumbling action in the cabinet helps in the recycling and reuse of blasting media. The media falls through the grates or screens at the bottom of the cabinet, and it can be collected, cleaned, and reused in subsequent batches, reducing media consumption and cost.
Automated Blasting Process: Tumble cabinets can be equipped with automated controls and timers, allowing for a repeatable and automated blasting process. This minimizes the need for constant monitoring and intervention during the blasting operation.
Enhanced Surface Coverage: The tumbling action ensures that the blast media reaches all nooks, crannies, and intricate features of the parts being processed, resulting in thorough cleaning and surface preparation.
Dust Containment: Tumble cabinets are designed with proper dust collection and ventilation systems, minimizing the release of dust and abrasive particles into the surrounding environment. This promotes a cleaner and safer working environment for operators.
Suitable for Delicate Parts: Tumble cabinets are ideal for delicate parts that require gentle handling during the blasting process. The tumbling action is less abrasive than other blasting methods, making it suitable for sensitive materials and fragile components.
Automotive and Aerospace Applications: Tumble cabinets are commonly used in the automotive and aerospace industries for cleaning and preparing small to medium-sized components, such as fasteners, nuts, bolts, brackets, and small engine parts.
Features and Considerations
Choose the appropriate abrasive blast media that can effectively remove coatings while being gentle enough not to damage the surface. Common blast media options include glass beads, aluminum oxide, and plastic media. The choice of media will depend on the type of coatings you are removing and the material of the components.
The blast cabinet should have adjustable pressure and flow control settings. This allows the operator to fine-tune the blasting parameters to suit different materials and coating types. Lower pressure can be used for delicate surfaces, while higher pressure may be required for stubborn coatings on sturdy parts.
An efficient dust collection system is crucial to maintain a clean and safe working environment. It prevents the accumulation of abrasive dust and removed coating particles, ensuring visibility inside the cabinet and reducing potential health hazards. Proper illumination is essential for inspecting and ensuring the quality of the blasting process. LED lighting inside the cabinet helps operators see the surface clearly and identify any defects or remaining coatings.
The blast cabinet should have durable gloves and armholes that allow the operator to manipulate the components inside while maintaining a sealed environment to prevent dust and media from escaping. Consider the size of the components you will be working with and ensure that the blast cabinet’s workspace is large enough to accommodate them comfortably. Look for a blast cabinet made from robust and durable materials that can withstand the abrasive nature of the blasting process.
A foot pedal control system allows the operator to start and stop the blasting process easily, providing better control over the operation. A regulator helps in controlling the air pressure, while a moisture trap prevents moisture from reaching the blasting media, ensuring consistent performance.
Safety should always be a priority. Ensure the cabinet has proper safety features like interlocks that prevent the door from opening during operation and protective gear to shield the operator from potential ricochets. Ensure that operators using the blast cabinet are well-trained in its operation and understand the importance of using the appropriate blasting parameters for different applications.
Final Thoughts
When it comes to blast cabinets, one size does not fit all. Blast cabinets come in a variety of sizes and types, and knowing which is the best fit for your operation will mean you acquire the correct equipment for your facility. For more than 70 years, the experts at N.T. Ruddock have been selling and maintaining blasting equipment as well as providing advice on their wide range of blast media. We’re happy to provide a consultation prior to purchase and support you with all of your blast cabinet needs!